We asked Peter Williamson to tell us a bit about the Muckle Tully sword.
The Muckle Tully hand forged sword and skeletal hand wall holder can be yours for £1,800 – the original price was £2,200.
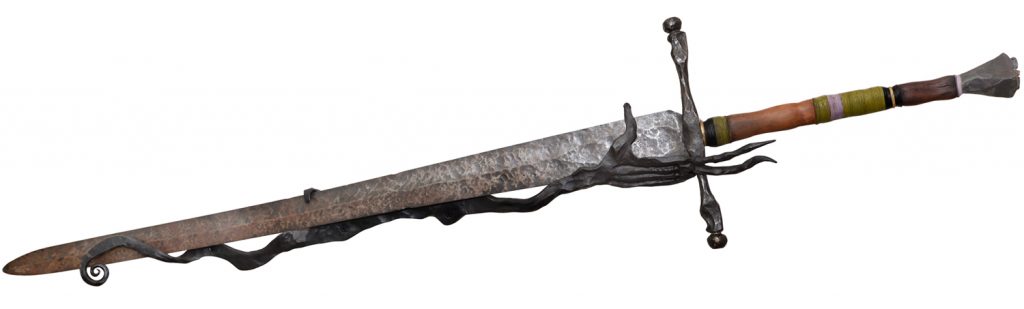
Why is the sword called Muckle Tully?
Both my parents and all the rest of my family come from Shetland, the northern isles, with the Atlantic to the west and the North Sea to the east. They speak English, but with a strong Shetland dialect, with old Norse, Scandinavian and Scottish words.
Muckle means big and Tully means knife – so the sword’s name translates to ‘big knife’ – that’s kind of what a sword is.
Here’s a map showing the Shetland islands (Shetlanders call it Shetland) in the centre, with the Faroe Islands to the north west, Norway to the east, the Orkney islands and Scotland to the south and Denmark to the south east.
Where did the idea of the sword come from?
The idea partly came from a desire to make the biggest sword that I could possibly make, partly from making a double handed sword and to see if I could play with proportions and volumetrics. Before I’d got very far with the sword, I’d drawn the size of the sword that I wanted to make on the chalk board.
The interesting thing is that the chalkboard is at home and the forge was four miles away in Bushey in Hertfordshire, so I didn’t have all that much opportunity to move the sword from the forge in Bushey to home. I decided to make it this size and by instinct and by choice of materials, I was able to pick the right amount of material and forge it to the shape.
When I got it home and started to put everything together, I held it up against the drawing and was amazed to discover that there was only half an inch of difference between the drawing and the sword that I’d forged.
Braveheart
Another influence was the film Braveheart, which I really liked when I was growing up, I wanted to make a bigger sword that the Braveheart sword – a really big sword!
What are the different parts of the sword?
You’ve got the pummel, a big tapered bit of mild steel, and then underneath that there are some brass and copper washers, then there is purple heart wood, then there are more brass and copper washers, and there are also some leather washers too, I found that they helped with compression.
Next to that is apple wood, then more brass washers, then there’s a large steel crossbar, which is hand forged to shape, then there’s the blade, the tang goes all the way through and there is a split pin underneath the pummel. It’s not necessarily traditional, but it’s an interesting style of construction.
What can you tell people about the shape of the sword?
I quite like the teardrop shapes for a sword. Rather than doing a fuller, it widens the blade out at the base, while still keeping structural integrity at the edge of the blade and then that tapers off into the cross-section and the diamond section of the rest of the blade. I like that it’s got minimal stock removal, so the shape almost entirely done by hammer. Bearing in mind that this sword is really quite long, the fact that it’s all done by hammer and hot forging, is quite a feat.
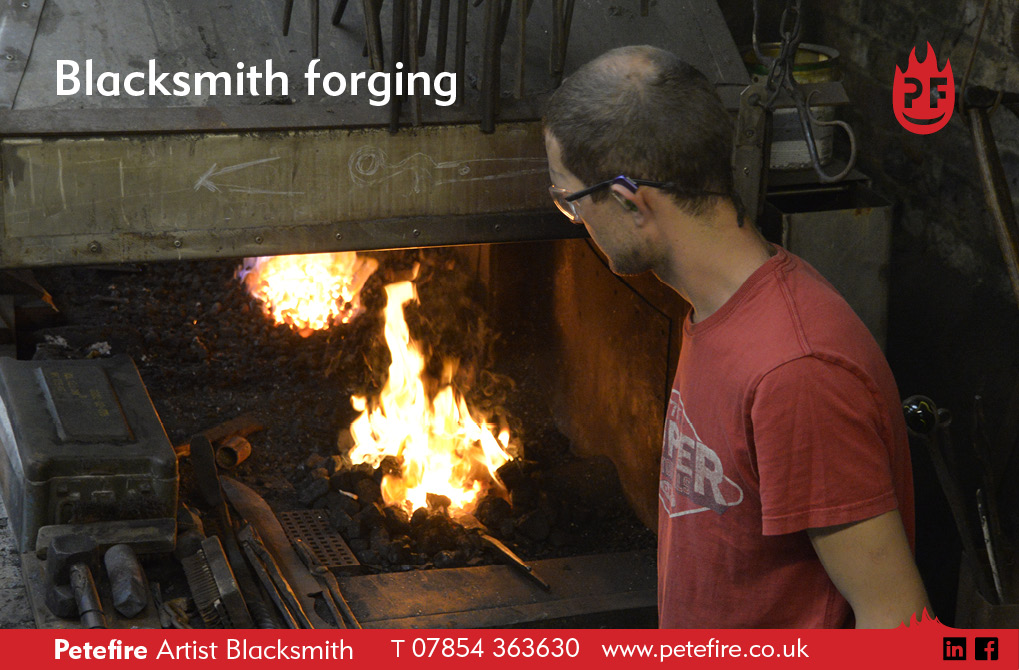
What is stock removal?
Stock removal is where you grind, file and sand off material. I kept this sword blunt, because I preferred it to be an ornament, or a piece of wall art.
Skeletal hand wall mounting
With that in mind I made a big steel skeletal hand as a sort of wall hanging scabbard for the sword to slide into, which is wall mounted.
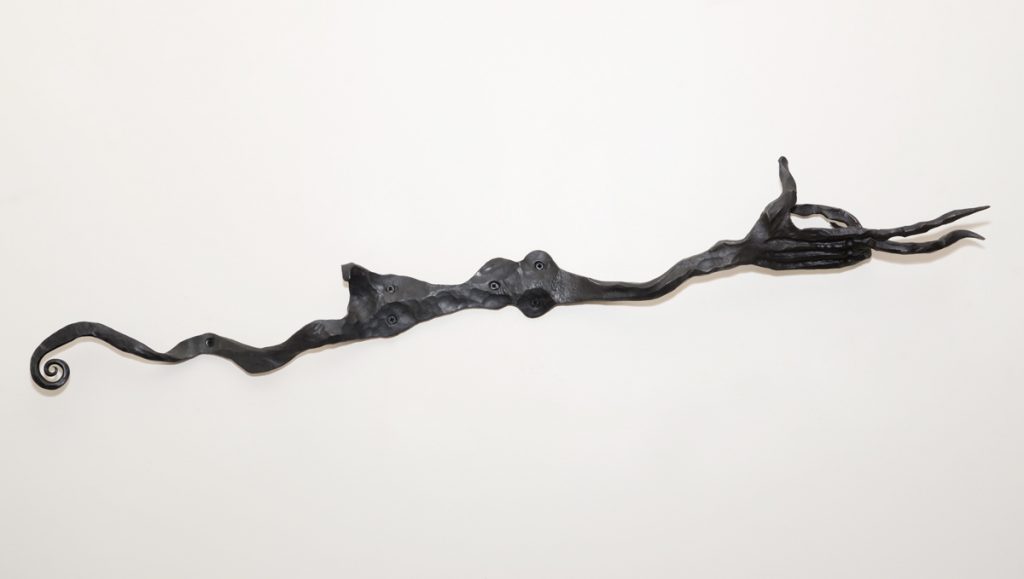
As part of the forging process for the skeletal hand scabbard I including a locking mechanism, where someone has to lift and twist the sword, before sliding it out of the scabbard. To get it out you are symbolically shaking the hand as you pull the sword out. It’s held next to the crossbar guard. The way that the fingers of the scabbard are positioned makes it impossible to remove it without doing the twisting action – it requires a little bit of dexterity and puzzling.
What’s the source of the metal?
The metal was repruposed from the compression piston from a digger. They have good volume and roundness, this kind of metal has good metallurgic composition. It can be used for sword making or other thing, for me it’s a nice ‘go to’ material.

The sword handle
It’s made from 2 different woods, purple heart and apple wood. I find apple wood to be very satisfying, it’s strong and good to work with, it looks good too. The apple wood was locally sourced – it came from a tree that had been felled at my previous forge in Bushey (south of Watford, Herts).
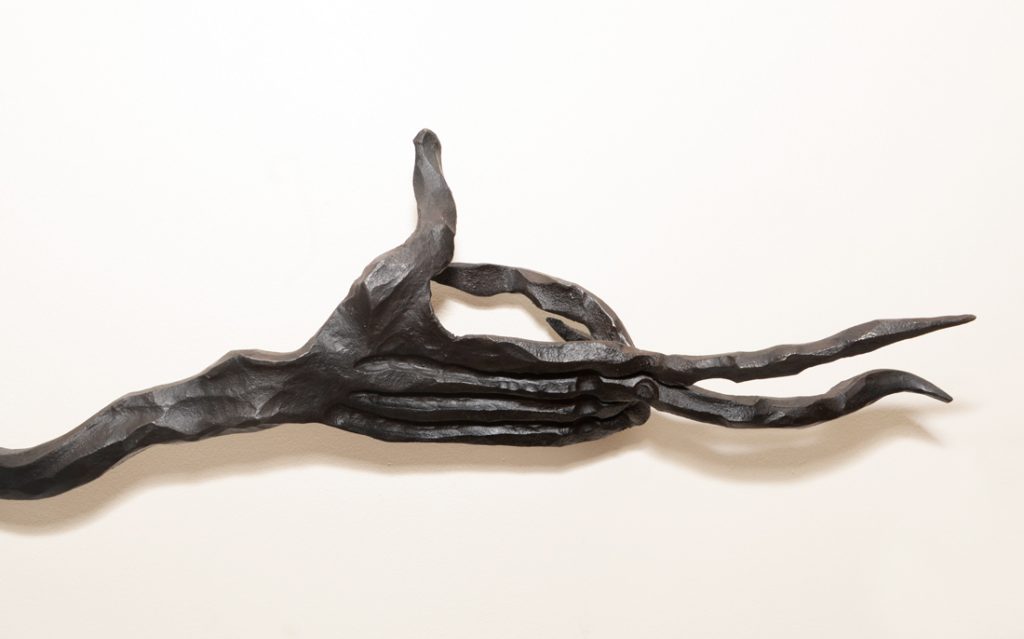
You can find out more about the wood I use here – based on my experience and what I’ve learned.
I was chopping up some wood for our wood burner – with one of the axes that I’ve forged. I realised that it was purple heart wood, which is one of my favourite woods. I checked one of the logs for cracks, realised that it was ok. This piece of wood really worked well for the Muckle Tully sword handle. I have also used purple heart wood from that set of logs for other sword and axe making projects.
We hope that you’ve found the interview about the Muckle Tully sword interesting – and that you’ve learned something new about sword forging.
The Muckle Tully hand forged sword and skeletal hand wall holder can be yours for £1,800 – the original price was £2,200.